What is anodised aluminium?
Widely used across many industries, anodised aluminium boasts enhanced durability, resistance to corrosion and aesthetic appeal. Through a process known as anodisation, the aluminium surface is transformed into a tough, protective layer, improving its performance and longevity. But what is anodised aluminium, and when should it be used?
What is anodised aluminium? The process, benefits and uses
As a go-to choice amongst engineers, designers and manufacturers, the use of anodised aluminium dates back around 100 years as a process initially developed to protect aluminium components in seaplanes from corrosion. Today, it’s used in a much broader range of applications, from architectural design and automotive to electronics and consumer goods. In this article, we’ll delve deeper into the process, why it’s so effective and how you can incorporate this material into your next project.
- What is anodising?
- How is aluminium anodised?
- How is anodising different from other finishing methods?
- What are the benefits of anodising?
- Where can anodised aluminium be used?
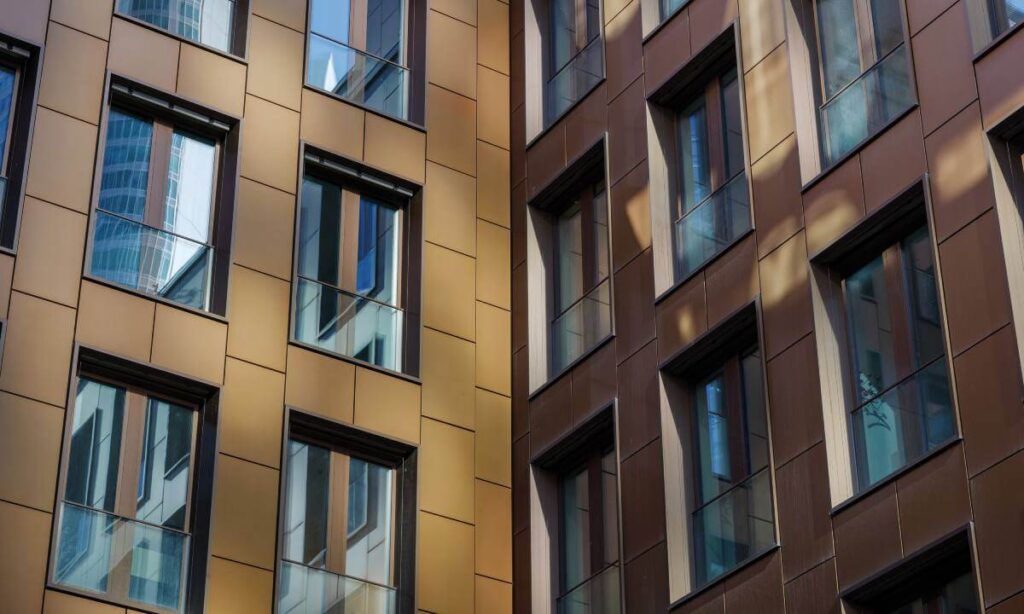
What is anodising?
Anodised aluminium refers to aluminium that has undergone an electrochemical process to enhance its natural oxide layer. During this anodising process, the aluminium surface becomes more durable, resistant to corrosion and capable of holding colour better, altering its aesthetics to meet its purpose.
But what do the electrochemical process and natural oxide layer really mean? Let’s break it down further. Electrochemistry is the process in which chemical reactions are driven by the movement of electrons through an electric current. The natural oxide layer is the very thin layer of oxide that naturally forms on the surface of any metal, including aluminium, when it comes into contact with oxygen in the air. Read on to learn more about how these processes are used when anodising.
How is aluminium anodised?
At Alanod, anodising remains one of the most common finishing methods amongst our clients who have a specific decorative finish in mind. The process is relatively simple and involves the following steps:
Pre-Treatment: Much like any finishing method, the aluminium must first be cleaned to remove dirt and grime from the surface. Depending on the desired results, the surface is then brightened (to achieve a metallic finish) or etched (to achieve a matte finish).
Anodising: Once prepped, the aluminium can now be anodised. This involves placing the aluminium in an acid bath (typically sulfuric acid) before applying an electric current. The surface is the aluminium is then focused to oxidise, forming a thicker oxide layer ready for colouring.
Colouring: As the oxide layer not only becomes thicker but also more porous, it can then be coloured using electro-colouring (used to achieve darker shades such as black, bronze and blue) or dyeing (ideal for providing a wider range of brighter colours).
Sealing: Finally, the aluminium is sealed to close the pores and improve its resistance to environmental damage, such as colour degradation, staining and scratching.
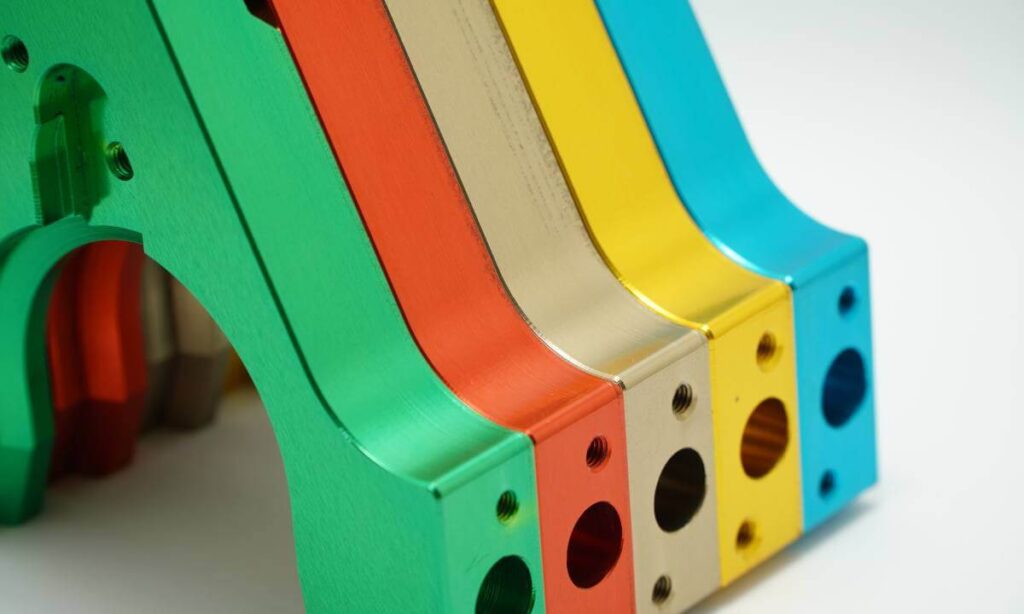
How is anodising different from other finishing methods?
While anodising remains one of the most widely used customisation techniques for aluminium, there are other finishing methods available based on your requirements and planned application.
When partnering with Alanod as your aluminium supplier, we can offer raw, anodised or lacquered aluminium. While anodising is best suited to applications such as building facades and interior design, lacquered aluminium is ideal for smaller details, including trims on cars, cookware and foil packaging. Why? Because lacquering can achieve a wide range of finishes such as soft, textured and diamond shine in a variety of colours, including dark shades such as anthracite.
Aside from anodising and lacquering, some of our clients opt to purchase raw aluminium from our team and then customise it during their own manufacturing process through powder or liquid paint coatings. For more information on all of the aluminium finishing methods mentioned, take a look at our previous article.
What are the benefits of anodising?
Due to its enhanced surface properties, anodised aluminium boasts a range of attractive benefits. These include the following:
Durable and long-lasting: As anodising creates a hard, protective layer, the aluminium is not only resistant to wear, scratches, and abrasion but also corrosion caused by moisture, salt, and chemicals.
Custom colour options: Anodising allows aluminium to be customised with many colours while still maintaining a smooth surface. From glossy or metallic to matte, there are a whole host of aesthetic options.
Lightweight and cost-effective: Particularly when using anodised aluminium in building design, the lightweight nature of the material will not only make installation far more straightforward but will also cut manufacturing, shipping and labour costs.
Environmentally friendly: The anodising process is non-toxic and produces no harmful by-products, making it an incredibly eco-friendly finishing technique. Once it has served its purpose, the anodised aluminium will also be 100% recyclable.
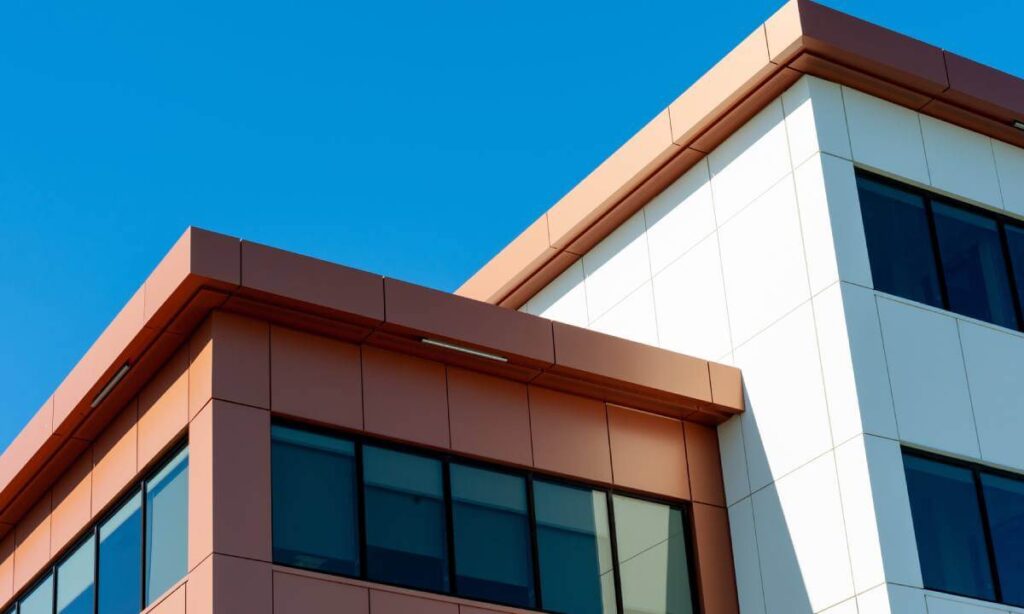
Where can anodised aluminium be used?
As briefly mentioned above, the robust, long-lasting, and aesthetic traits of anodised aluminium make it an excellent building material. Its weather resistance and long-lasting colour retention are ideal for exterior cladding, window frames and doors, while its strong and lightweight nature makes it perfect for railings and handrails. Aside from this, anodised aluminium can be used for many further applications, such as:
- Vehicle trim and body components
- Aircraft interior panels and structural parts
- Smartphone and laptop casing
- Decorative interior wall facades
- Boat railings, masts and components exposed to salty water
- Outdoor signage displays
The possibilities are endless!
If you have a project in mind and are considering incorporating anodised aluminium or would like to learn more details, please do not hesitate to contact Alanod. With over 40 years of experience supplying metal surfaces on a global scale, we will work closely with you to tailor our supply services to your needs. Whether you require a single sheet or high-volume production runs, our UK team can meet your demands with quality, reliability and professionalism.