Aluminium – forming our future?
The first successful attempt to create aluminium happened almost 200 years ago. At the time aluminium was considered more precious and rarer than gold, however, thanks to techniques that were developed to produce it more cost-effectively, it is now one of the most versatile metals in manufacturing.
Why has it become so popular? The answer can be found in the wide range of advantages that aluminium offers. It is:
- Corrosion resistant
- A high thermal conductor
- Non-magnetic
- Lightweight but durable
- Strong and impermeable
- An excellent heat and electrical conductor
- Simple to process
- A good reflector of light and heat
- 100% recyclable
- Cost effective
- Strong at low temperatures
- UV-resistant
Versatility at its core
Aluminium can be supplied in a variety of grades and depending on the alloy present, each grade has certain, unique characteristics. For example, aluminium-magnesium-silicon alloys are ideal for use in applications where lightweight strength is essential, such as automobile body sheets. As well as being able to machine and form it, aluminium can also be cast and melted.
Here at Alanod, we process more than 10,000 tons of aluminium a year and by using different techniques, create a wide range of high-tech surfaces. To achieve this, we use:
Anodising – The surface of aluminium can be transformed into aluminium oxide (Al3O3) through the electrical oxidation of the metal’s surface. Unlike lacquer coatings, the resulting anodic layer is an integral part of the material and it is used wherever a long-term stable, resistant surface and decorative appearance is required. Incorporating colour pigments during the anodising process also produces stable coloured surfaces. Applications include refined design-oriented decorative and functional aluminium surfaces for both interiors and exteriors.
Vacuum coating – Physical Vapour Deposition (PVD) is a process where metallic materials are vaporised, and the resulting metal atoms condense on the substrate to form thin layers. The end result is decorative surfaces that also have excellent mechanical properties. It is not surprising therefore that PVD-treated aluminium is frequently used in electronics, lighting and solar industries.
Primer lacquer systems – Aluminium can be refined with highly transparent, clear lacquer systems by roller application. This improves the anti-corrosion protection of its surface, with only a minimal reflection loss. Opaque or translucent cured lacquers can give a unique decorative character and other functional benefits, such as scratch and chemical resistance and anti-fingerprint properties. By applying a special primer, it is also possible to laminate the aluminium with phenolic resin impregnated kraft papers.
Technologies such as anodising, lacquering and vacuum coating can be refined using a continuous coil-to-coil method to deliver impressive properties such as scratch resistance, anti-fingerprint technology, good plasticity and easy printability. With process combinations continually being refined, many industries are benefitting from these innovative surface solutions.
Almost 200 years on, the uses for aluminium are still being explored. In conjunction with strategic partners from the worlds of plastics, mechatronics, electronics and the lighting industry, we are creating functional metal-hybrid technologies for the future. So, whether you are looking for a state-of-the-art solution, or a standard surface modification, why not find out more about how aluminium could be used to help you with your specific application?
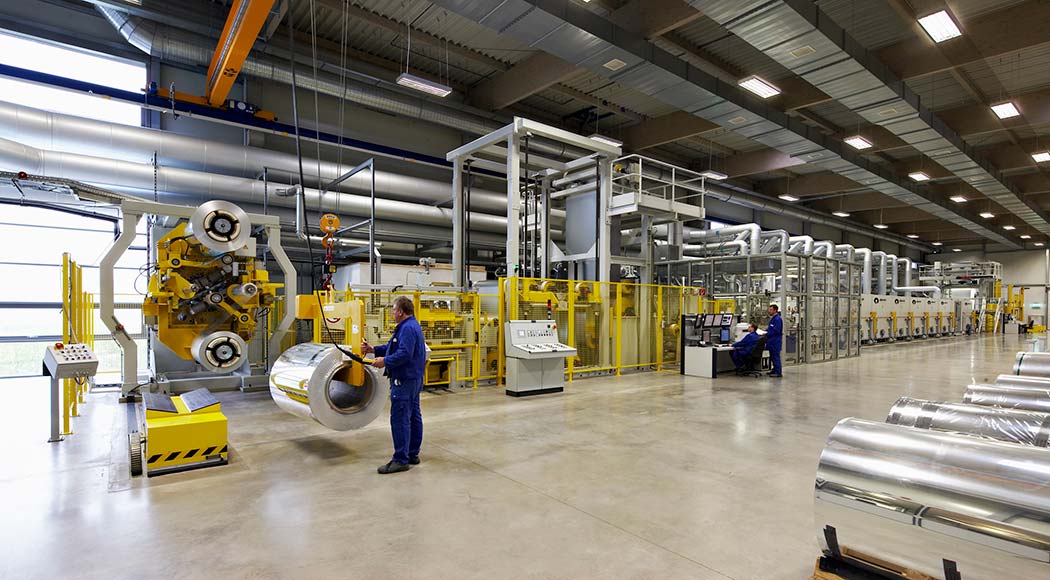