What is PVD coating?
As an advanced surface treatment, PVD creates an ultra-thin yet robust layer that bonds at an atomic level, ensuring maximum performance without adding bulk. Its durability, wear resistance and aesthetics have revolutionised how materials are protected and finished. In this article, we’ll explore how PVD coating works, its benefits and why it’s the preferred choice for high-performance applications.
What is PVD coating? Definition, benefits and uses
From aerospace and automotive components to luxury watches and medical instruments, PVD coatings are used across many applications. At Alanod, we have spent over 40 years supplying aluminium on a global scale and actively use PVD coatings in our solar absorber surfaces. Learn more about our surfaces and how they can be used to innovate your product design.
- What is PVD coated?
- How does PVD coating work?
- What are the benefits of PVD-coated materials?
- How do we use PVD coatings at Alanod?
What is PVD coated?
Physical Vapor Deposition (PVD) is a high-performance, vacuum-based finishing process designed to enhance durability, appearance and performance. While it is most commonly used on metals, PVD coatings are suitable for many materials, including ceramics, glass and plastics.
Unlike traditional coatings such as electroplating or painting, PVD forms a molecular bond with the surface, offering a much higher durability and scratch resistance. This makes it ideal for many applications, such as watches and jewellery, automotive parts, tools, medical instruments and, at Alanod, our solar absorber surfaces.
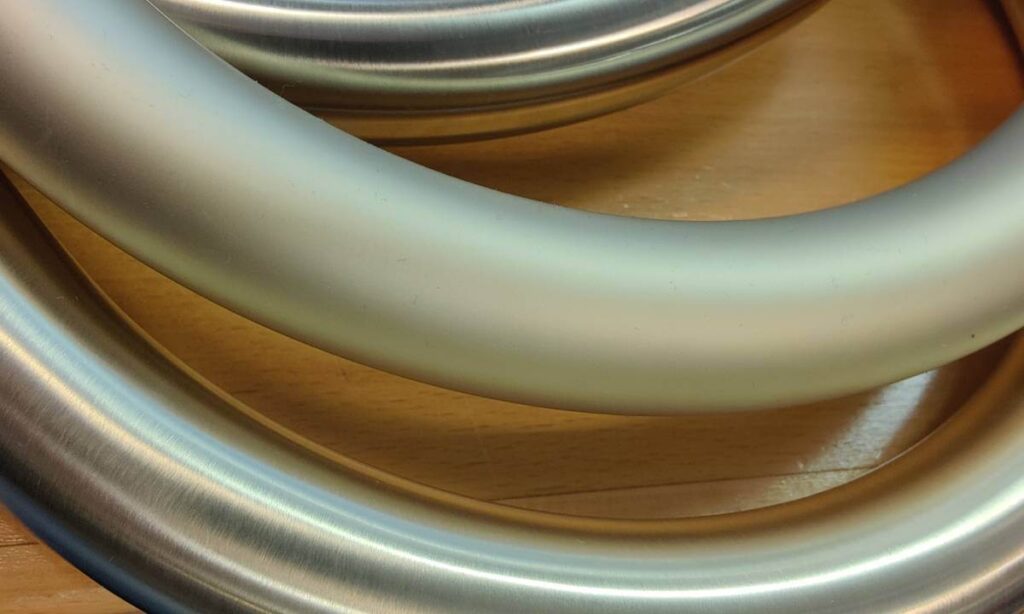
How does PVD coating work?
The purpose of PVD coating is to create a thin film of hardened particles over the surface; here’s how it works:
- Preparation: The substrate (material to be coated) is first cleaned and then placed in a vacuum chamber to remove dust, dirt and oxides, ensuring maximum coating adhesion.
- Vaporisation: Whilst in the chamber, a solid metal is heated to extremely high temperatures (vaporisation) using electron beams (thermal evaporation), by bombarding it with ions (magnetron spluttering) or through a high-energy electrical discharge (arc discharge).
- Deposition: The vaporised metal reacts with gases inside the chamber, which forms a thin, solid layer of metal compound that deposits onto the surface and creates an incredibly durable film.
- Cooling and finishing: The coated material is left to cool down, and if requested, an additional finished process, such as polishing or buffing, can be applied.
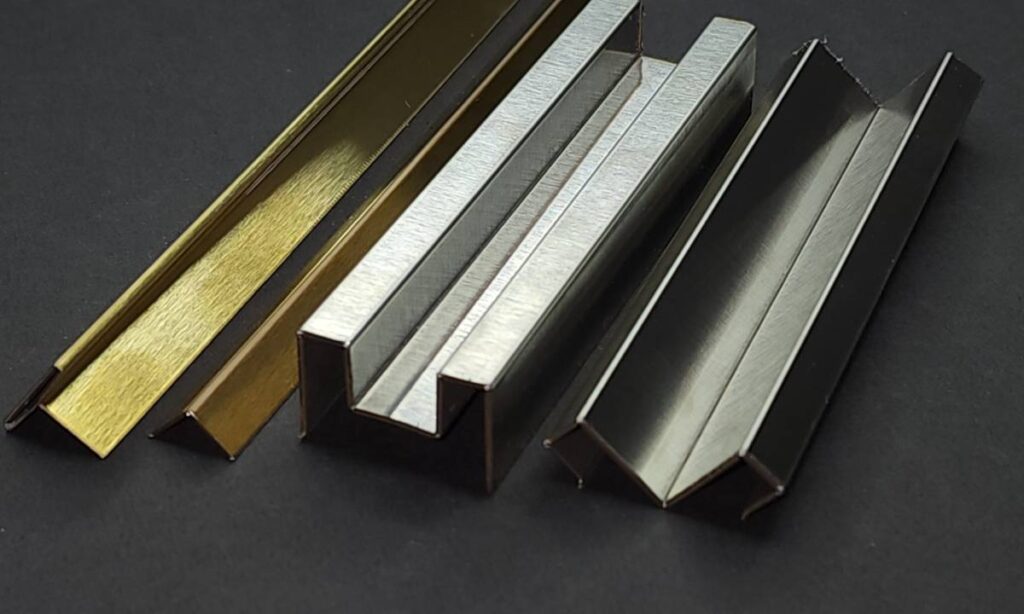
What are the benefits of PVD-coated materials?
The wide-ranging benefits of PVD coatings make them a top choice for industries seeking to enhance product durability, performance, and aesthetics. Key advantages include:
Environmentally friendly and non-toxic
Unlike traditional plating methods, PVD coating does not involve any hazardous chemicals or produce toxic waste. This not only makes it an excellent choice for those aiming to meet their sustainability goals but also for companies searching for a food-safe coating.
Extremely hard-wearing and wear-resistant
As mentioned throughout, surfaces treated with a PVD coating are significantly more hard-wearing than those without. The protective barrier created during the process shields the underlying metal from abrasion, scratches and chemical damage. This improves performance, improves longevity and reduces maintenance costs.
Customisable to suit different aesthetics
One benefit we have yet to mention is the aesthetic attributes of PVD coatings. Different metals and gases can be used to create unique finishes in various colours and textures, such as gold, black, rose gold, bronze and silver. Not only this, but unlike traditional paint or plating, the appearance achieved through PVD will not fade, chip or peel.
Wide applications across many sectors
With the above benefits in mind, it is clear that PVD has become one of the few coatings that bridge the gap between industrial-grade performance and high-end aesthetics, which makes it suited to many industries. While we briefly listed some examples above, PVD coatings are also regularly used in the medical industry for surgical instruments and implants, aerospace for turbine blades and engine components, and electronics for smartphones and wearables.
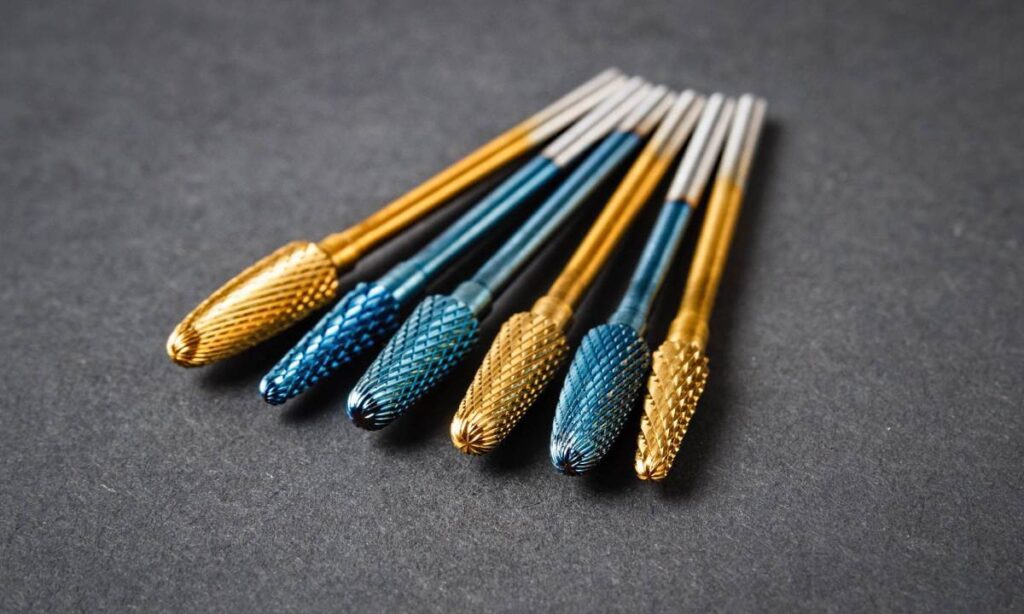
How do we use PVD coatings at Alanod?
As an industry leader in aluminium and metal surfaces, we use several coating and finishing methods to tailor our products to their applications. PVD coating is used for our solar absorber surfaces and is designed to offer a high thermal or solar energy absorption level with low thermal emissivity. Our options include:
eta Plus®
Used for flat-plate collectors, tube collectors and façade collectors, eta Plus® is available in copper and aluminium. The coating offers a 96% solar absorption rate with only 4% thermal emissivity. It’s applied using a continuous PVD method through an air-vacuum-air process, and once manufactured, it is suitable for both laser and ultrasonic welding.
mirotherm®
Ideal for solar thermal systems, mirotherm® coatings are a three-layer absorber system based on an aluminium strip capable of both absorbing direct sunlight and diffusing radiation. It is designed with:
- An IR-reflective layer to ensure thermal emissivity
- Oxide absorption and anti-reflection coatings for maximum solar absorption and resistance to external influence
- A laser-weldable anti-corrosion coating
mirosol® TS
Our mirosol® TS coating is manufactured using a specialised process that applies a selective, hydrophobic lacquer, making it best suited to solar thermal systems placed in regions with high solar radiation. Available on aluminium, mirosol® TS is resistant to heavy environmental pollution, salty air, moisture, condensation, low stagnation temperature, oil and dirt.
mirotherm® Control
Our final solar absorber surface is mirotherm® Control, which offers all of the same traits as our best-selling mirotherm® but with integrated protection against overheating. It has a reverse side optimised for laser welding and up to a 40°C lower stagnation temperature compared to standard systems.
For more information on our solar absorption surfaces and how they can be used, take a look at our previous article or feel free to contact us to discuss how we can support your business.
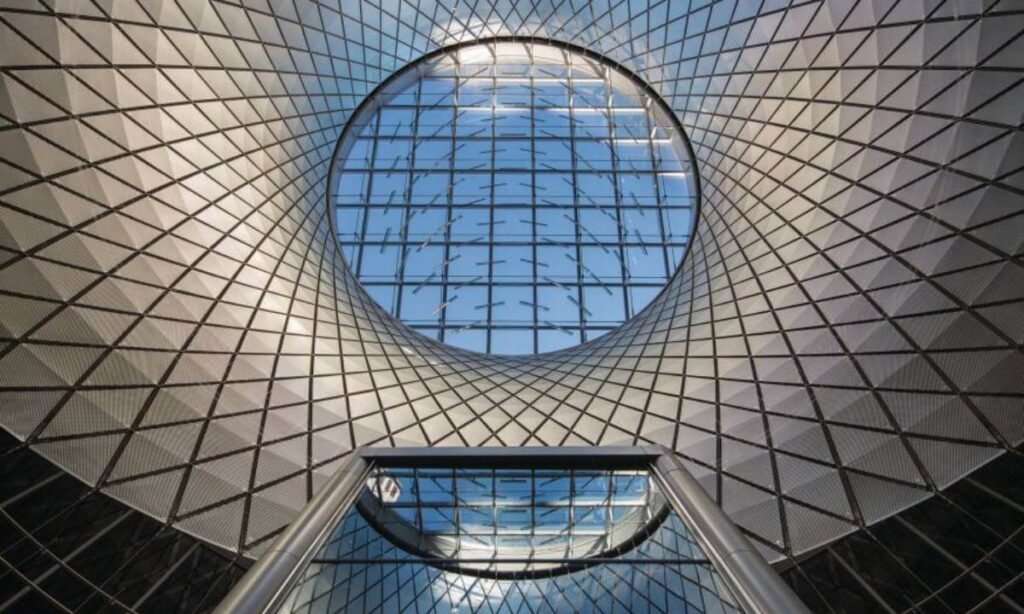
Utilising PVD to achieve stronger, sleeker and longer-lasting surfaces
Able to maximise product lifespan and improve aesthetics while remaining environmentally friendly, it is no surprise that PVD appeals to many industries. As a superior alternative to traditional coatings such as electroplating and powder coatings, the capabilities of PVD will continue to grow as technology advances.
If you have any further questions regarding PVD coatings or would like to discuss our solar absorber surfaces, please do not hesitate to contact our team. With decades of experience, we tailor our supply to your requirements, ensuring maximum performance and longevity.