Solar absorption – maximising efficacy
With government policies driving investment in all kinds of renewables, the efficacy of solar energy generation – in all its forms – is something of vital importance to profitability. To ensure maximum efficiency in solar absorption equipment, the secret lies in the efficiency of the solar collector equipment’s coating.
Solar thermal collection
There are two primary types of solar collection:
- Flat plate solar collectors are the most common form and they first made their appearance over 70 years ago, being used to heat domestic hot water.
- Evacuated tube solar collectors are more expensive options, but can achieve higher temperatures than their flat plate cousins.
- There are also a range of more unusual solar collectors such as concrete and asphalt heat absorption solutions.
Absorption coatings 101
When it comes to solar absorption efficiency, the collector, or absorber plate is key to ouput. Typically it is made from copper, stainless steel or plastic, and is enclosed within a black casing to maximise absorbance. By coating the absorber plate with a selective coating made from copper, aluminium or mild steel and a specific coating, absorptivity can be increased still further.
Why do absorber plates (or tube collectors) use a selective coating?
To achieve increased energy conversion efficiencies the absorber plate must have a coating that features selective properties. Key to efficiency are coating properties that minimise reflectance in the infrared region, whilst also maximising absorption of radiation in the ultraviolet, visible and near-infrared spectra. These properties can be adjusted, depending on the application they are being used for.
High temperature and selective absorption coatings
High-temperature solar selective absorbing coatings (HTSSACs), such as silicon hybrids, are also available and can increase the harvested solar energy from the thermal receiver of next-generation concentrated solar power systems. They typically operate at temperatures of more than 700oC. However, thermal stabilisation and corrosion resistance are some of the aspects of these coatings that can still cause challenges.
PVD-coatings using the air-to-air process vs absorbing lacquer applied in the coil-coating process.
Thin-film coating, also known as PVD (physical vapor deposition) coating, enables a solid material to be vaporized in a vacuum and deposited onto the surface of a part. The end result is a thin, bonded metal or metal-ceramic surface that improves the function of the thermal absorption surface. PVD application processes include sputtering and evaporation. The former creates improved film quality and uniformity but is more costly than evaporation.
Alanod absorption coatings
Alanod’s selective absorber coatings have solar absorption rates of up to 97% and emission rates as low as 4%. They are all backed by a 10-year outdoor material warranty.
Alanod offers coatings to suit a wide range of applications, including temperature fluctuations and tough external conditions – such as heavy environmental pollution, salty air, moisture, condensation, oil, and dirt as well as a low stagnation temperature.
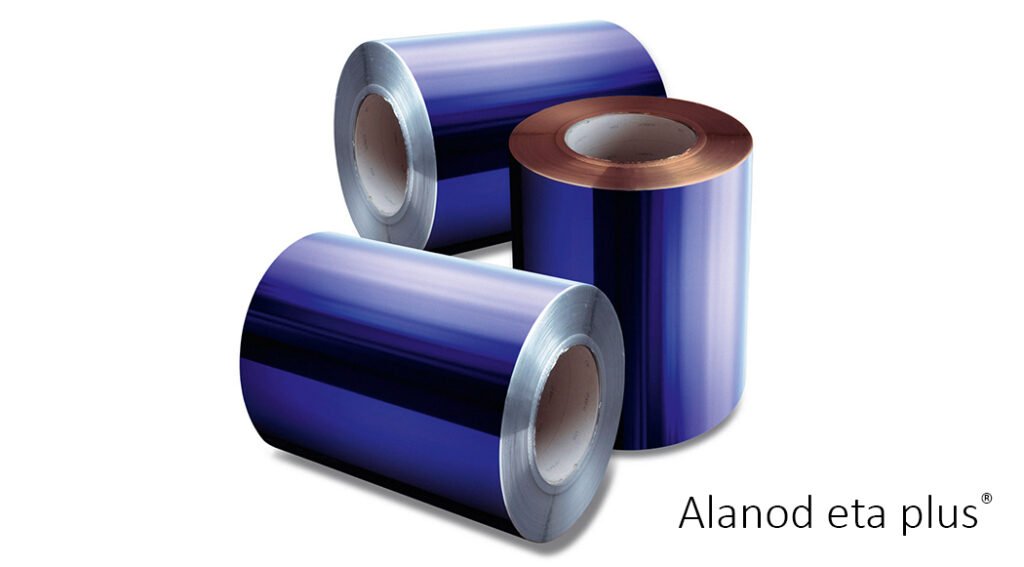
eta plus® achieves a very high solar absorption of up to 96% – combined with a very low thermal emissivity of just 4%. Based upon an aluminium or copper strip, the innovative, absorber layer system is applied using a continuous PVD method in a worldwide, technologically unique air-vacuum-air process.
Getting the right solar absorption coating is important, as it can have a significant impact on the solar yield of a plant or an individual installation over the course of its lifetime.
To find out more about Alanod’s solar absorption materials visit our solar page.